Prefab Container House VS Ordinary Cubicle
–Five Core Differences Analysis, Teach You How to Choose a Better Temporary Building Program
I. Introduction: The Dilemma of Choice Under the Demand for Temporary Building
In scenarios such as site construction, exhibition building, and field operations, the demand for temporary buildings is growing rapidly. However, many people have ambiguous perceptions about the differences between container houses and ordinary cubicles. What are the essential differences between these two seemingly similar temporary buildings in terms of structure, performance, and application scenarios? How can we make a better choice based on actual needs? This article will analyze five core dimensions to provide you with professional decision-making references.
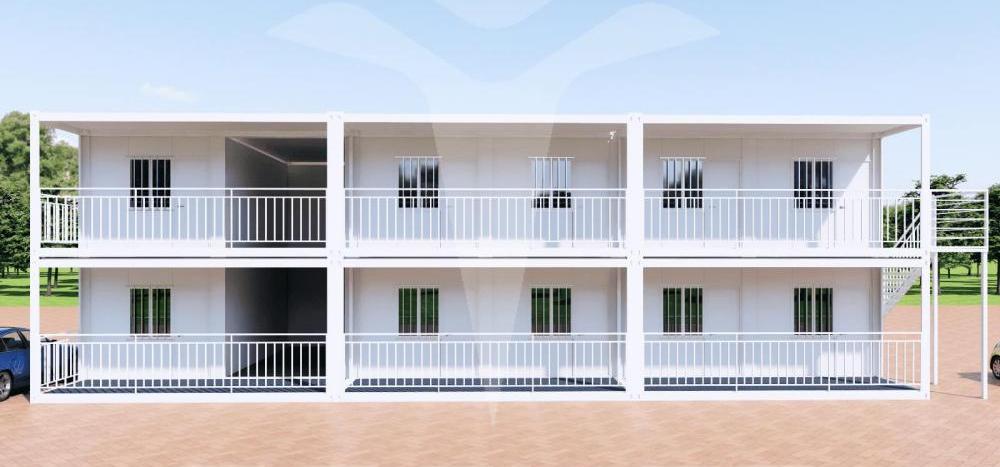
II. Structure and Materials: See the Essential Differences from the "Foundation"
(A) Container Housing: The Hard Core Strength of the Industrial Skeleton
Core Structure: Built with an ISO-standard container frame, welded by Q235B/C high-strength steel, forming a “steel box” structure.
Wind & Earthquake Resistance: Withstands wind forces ≥ Grade 10 and anti-seismic intensity ≥ 7 degrees.
Wall Materials: Customized color steel sandwich panels (≥0.5mm steel thickness), filled with fireproof and thermal-insulating materials like rock wool or polyurethane. Sealing performance meets IP54 standards (dustproof and waterproof), resistant to acid-base corrosion, suitable for harsh environments like coastal areas.
(B) Ordinary Cubicle: The Limitations of Light Steel Structure
Frame Design: Light steel keel + C-beam structure, with steel thickness mostly 0.3-0.4mm, prone to deformation under long-term load.
Wall Defects: Foam-filled color steel sandwich panels (≤0.4mm steel thickness), poor joint sealing leading to rain leakage in wet seasons and heat loss in winter.
Safety Risks: Weak structural stability, vulnerable to strong winds or geological disasters.
III. Functional Performance: Core Gaps in Use Experience
(A) Mobility: "Move-as-You-Go" VS "Demolition and Construction Project"
Comparison Dimension | Container House | Ordinary Cubicle |
Relocation Method | Whole-container lifting, 4-hour transfer | Piece-by-piece disassembly, 2-3 days |
Transportation Cost | ~¥800-1,200 per container | 15%-20% material loss, +30% cost |
Ideal Scenarios | High-frequency relocation (e.g., exhibitions, rescue camps) | Fixed-site long-term use |
Key Insight: Container houses’ modular design enables quick crane relocation without on-site disassembly, saving time and reducing material waste.
(B) Sound Insulation and Thermal Insulation: The Watershed of Living Comfort
Container House:
Double-layer sandwich panels + acoustic cotton: Sound insulation ≥25dB (blocks upstairs footsteps and external noise).
Thermal insulation layer (50-100mm thick): K-value ≤1.5W/(㎡·K), creating 8-10℃ cooler summers and 5-7℃ warmer winters.
Ordinary Cubicle:
Single-layer wooden board + foam: Sound insulation ≤15dB (audible conversations through floors).
Thin foam insulation: Only 3-5℃ indoor-outdoor temperature difference in summer, high air conditioning costs.
(C) Service Life: The Trade-off Between Short-Term Investment and Long-Term Cost
Container House: 20-30 years lifespan, recyclable ≥5 times, cost-effective over time.
Ordinary Cubicle: 10-15 years lifespan, ≥50% material loss after 3 disassemblies, risking total scrapping and higher reconstruction costs.
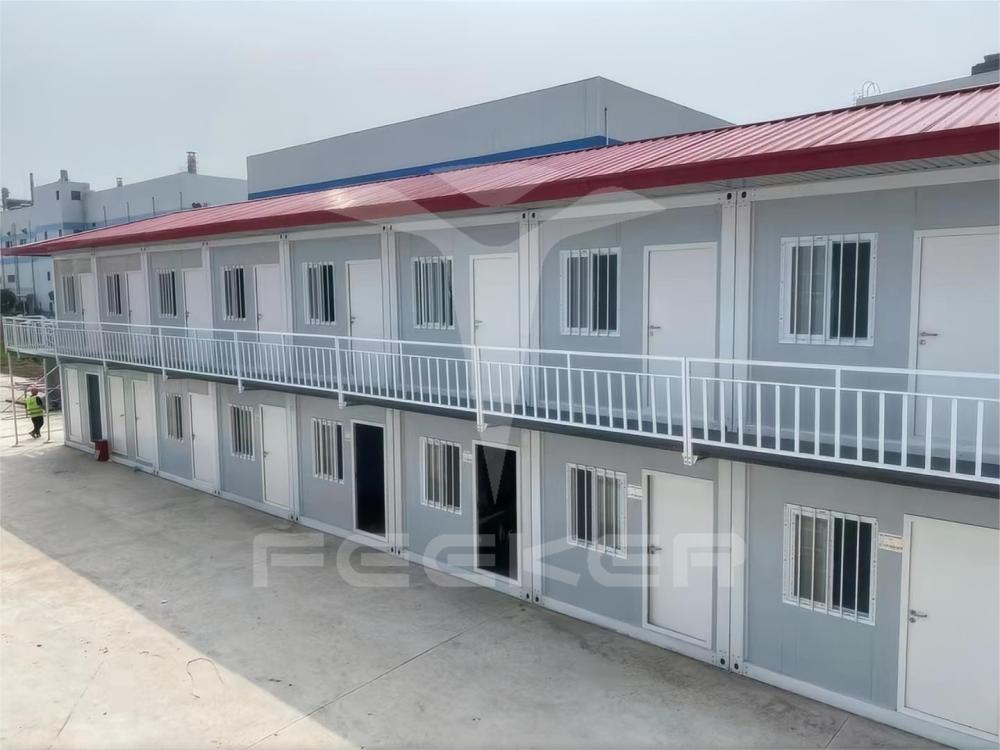
IV. Environmental Friendliness: Considerations from a Sustainable Development Perspective
(A) Resource Utilization Efficiency
Container House:
70%+ recyclable materials (90% steel recycling rate).
Modular production reduces construction waste by ~50 tons per 1,000㎡ compared to traditional cubicles.
Ordinary Cubicle:
~2 tons of construction waste per disassembly.
Annual timber consumption equivalent to 5,000 trees for 100,000㎡ cubicles, straining ecosystems.
(B) Energy-Saving Performance Comparison
Container House: Energy-efficient doors/windows + thermal systems reduce annual energy consumption by ≥40%. Pairing with solar panels achieves “net-zero energy”.
Ordinary Cubicle: No systematic energy-saving design, with air conditioning accounting for 60% of operational costs and higher carbon emissions.
V. Guide to Applicable Scenarios: Decision Tree for Demand Matching
(A) Six Scenarios Prioritizing Container Houses
Construction Sites: Relocatable project offices and dormitories (safety + efficiency).
Cultural Tourism: Customizable temporary lodges and camping bases in scenic areas.
Emergency Rescue: Rapid-deployment shelters in disaster zones (earthquake/flood resistance).
Commercial Pop-Ups: Brand exhibition booths and market stalls (flexible nationwide relocation).
Municipal Projects: Long-term office command centers for subway construction (comfort-focused).
Field Research: Workstations in extreme environments (weather resistance).
(B) Suitable Boundaries for Ordinary Cubicles
Short-Term Use (≤2 years): Temporary warehouses or simple sheds in fixed sites.
Low-Requirement Storage: Material storage without sound/thermal insulation needs.
Tight-Budget Projects: Short-term transitions without long-term recycling plans.
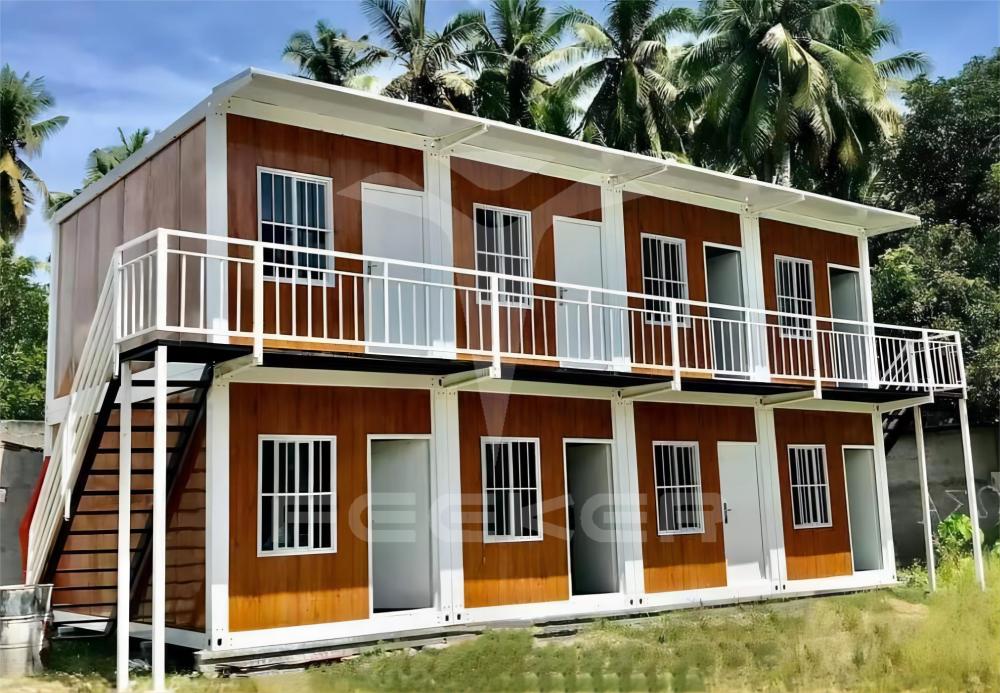
VI. Purchase Pitfalls to Avoid: Three Core Quality Indicators
(A) Steel Test Reports
Key Metrics: Verify yield strength (≥235MPa), tensile strength (≥370MPa), and hot-dip galvanization thickness (≥80μm, 10+ years anti-rust).
Risk Avoidance: Reject non-standard steel to prevent structural failures.
(B) Sandwich Panel Combustibility
Safety Mandate: Use Class A non-combustible materials (rock wool/glass wool) in crowded areas (e.g., construction dormitories).
Hazard Warning: Avoid B3-grade flammable foam panels (release toxic gases when burning, linked to safety incidents).
(C) Manufacturer Qualifications
Certifications: Prioritize ISO9001-certified suppliers.
Due Diligence: Request past project case studies or on-site inspection reports to avoid unqualified “guerrilla” contractors.
VII. Trend Insight: The Future Evolution of Container Housing
(A) Smart Upgrades
Integration of solar power, intelligent temperature control, and IoT monitoring for remote management.
(B) Modular Customization
Expandable container house designs (e.g., hydraulic extension) to triple usable space per container, adapting to diverse needs.
(C) Green Certification
Rising adoption of LEED and China Green Building Materials certifications, aligning with “dual-carbon” goals.
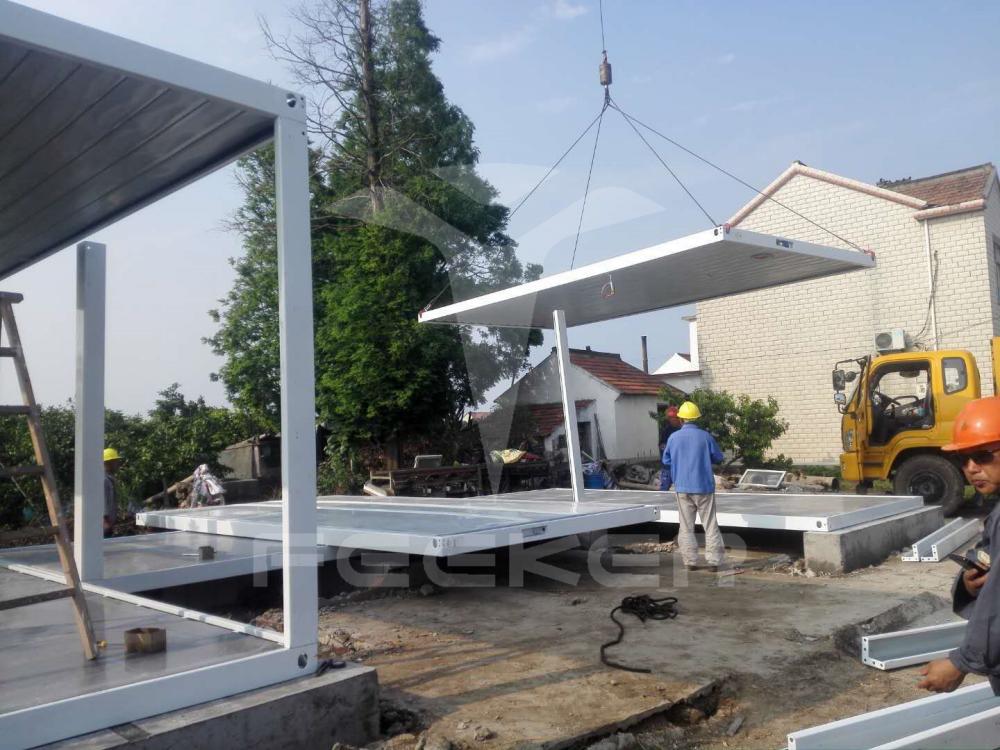
VIII. Conclusion: The "Long-Termism" Choice in Temporary Construction
The contrast between container houses and ordinary cubicles reflects a fundamental shift from “temporary fixes” to “industrial-grade quality”. With superior safety, durability, and sustainability, container houses offer long-term value by reducing lifecycle costs and enhancing usability.